ERP solution for Manufacturing industry
Manufacturing, with its intricacies of materials, processes, and workforce, is the epicenter of the global economy. Companies that succeed in this field are those that embrace the most advanced technologies to optimize their operational efficiency.
ERP emerges as a crucial pillar, providing a suite of integrated tools to plan, execute, and control every aspect of production. Join us as we explore how ERP is shaping the future of modern manufacturing and how it can propel your business to new heights.
What is manufacturing?
Manufacturing is the process of transforming raw materials into a finished product or goods. The creation of these products can be done by hand or by machine, and once completed, they are sold to consumers or other businesses for various purposes.
The goods created can also be part of a larger product. Companies use manufacturing ERP software to help manage, plan, and support these activities. They also play a role in the following to help businesses evolve, reduce expenses, and increase production quickly and efficiently.
The ERP software helps to :
- Plan materials, orders, resources, and more. Your MRP, Quality, Maintenance, and PLM applications are fully integrated on one platform.
- Control your production : The ERP software gives you more control over key manufacturing areas, quickly correcting and synchronizing your technical changes, Bill of Materials (BOM), and routing to increase responsiveness to customer demand.
- Optimize your inventory level: Keep inventory under control with automated actions, threshold levels, and predefined inventory rules. Your master scheduler calculates everything for you. Use routes, constraints, and lead times to optimize stock levels and avoid shortages.
WHAT ARE CONNECTED APPLICATIONS WITH MANUFACTURING ERP?
Manufacturing ERP software integrates manufacturing, inventory, sales and workforce management, as well as accounting to help businesses ensure raw materials are in place and available for product production, but functionality does not end here. The Odoo ERP software, for example, manages the entire manufacturing process, from the creation of your bill of materials to the automated re-ordering of materials when stock is low. With traceability, your products can be traced all the way back to their component parts lot number. Because of its connection to sales and accounting, ERP software ensures that your financials are accurately automatically recorded to track cost and profitability. Through these and various other features, ERP software is able to successfully manage and automate important manufacturing activities.
ERP for Paint Manufacturing: How Factory ERP Can Help Manage Unique Production Processes
One example of factory ERP is ERP software for manufacturers in the paint industry. Paint manufacturing requires a unique set of processes and procedures, which can be effectively managed by ERP software tailored for this industry. ERP for paint manufacturing can help businesses manage their inventory, production processes, and quality control, while also improving customer satisfaction through faster delivery times and higher quality products.
The key features of an ERP system for manufacturing
An ERP system for this sector offers many functionalities designed to meet the complex management needs of resources, production, and logistics unique to this industry.
Material and Order Management
BOM (Bill Of Materials)
The bill of materials, or BOM, is the description of the components needed to build a product. For example, let's say we had to build a table. The BOM would indicate you need a tabletop, four legs, and some screws to assemble the table. Since each individual component can also have its own bill of materials, there are what we call bill of materials levels. Each with its own set of sub-components. Similarly, a sub-component can also have its own bill of materials, creating multiple levels of bill of materials. This feature is very important, but it's a functionality that some ERP software doesn't handle properly. However, this feature is included in Odoo ERP software, and you can manage as many different levels as needed.
Work Orders
Work orders are documents provided to the manufacturing workshop as signals to produce a certain quantity of a specific product. The work order includes your bill of materials and routing. In other words, it will provide the materials and assembly processes for a product. The system will create an individual work order for each operation and their respective work centers in your ERP. So, to go back to our table example, there will be one manufacturing order and three work orders to assemble the table.
Principal Master Production Schedule
The ERP software gives manufacturing facilities the ability to create a master production schedule. A manufacturing center may receive multiple production orders at once, so it's important that everything is created and managed on time. A master schedule allows you to allocate work properly based on the current workload and the capacity of your manufacturing work centers.
Production Control
Routing
Routing is a description, or a roadmap, of the processes that need to be followed to assemble a product. The descriptions are arranged in order based on how a product should be built. For example, with our table, there's a specific process to follow, starting with assembling the table (attaching the tabletop to the legs), then painting the table, followed by varnishing, and finally packaging. Each operation will be handled by a particular work center, and some operations may also be outsourced and performed outside your company. These outsourced tasks can also be managed within the ERP software.
Quality Controls
In addition to routing operations, another step performed is quality assurance. Quality controls can be carried out in several ways:
- Visual inspection : examining the object to see if it is correctly constructed.
- Image verification: Assessing quality based on the appearance of the finished product in an image.
- Dimensional checks: Quality control based on the dimensions of the finished product compared to the routing description. This can be measured manually or with connected tools such as IoT-enabled cameras, etc.
PLM (Product Life Management) et Ingénierie Produit
PLM, or Product Lifecycle Management, is a method of managing the entire lifecycle of a product. PLM encompasses everything: from design, engineering, manufacturing, sales, and service of a product until it reaches its destination in the supply chain. Similarly, product engineering is particularly intriguing as it pertains to how we build a product. It can be understood as synonymous with PLM.
- Technical change order : Continuing with our table example, let's say several customers have left negative reviews about your table and are deciding to return it because it's broken. This may indicate that something needs to be changed in product engineering. Here, you can attempt to modify the bill of materials, or the routing based on the identified problem area. In a newly created technical change order, there will be a list of steps to improve the table's manufacturing. These are called Bill of Materials (BOM) Modifications and Routing Modifications. This change of order will be the initial step to authorize changes to the materials and/or processes used to manufacture a product.
Traditionally, product engineers would consider these new changes and review cost control and sales. Cost control will ensure that the item remains competitively priced in the market, and sales control will ensure that this price is adjusted accordingly based on other market competitors. Engineers will also conduct a quality standard check, determining if the product meets what is typically expected for a given product. - Tracking engineering orders with effective dates : An effective date or effective start date indicates when the changes identified in a technical change order will be valid. All existing orders prior to this modification will continue to use the original bill of materials and routing sheet until the effective date.
Human Resources Management
Employee Monitoring and Performance
Human resource management is a crucial element in any business, especially in manufacturing. ERP systems integrate specific functionalities to track and evaluate employee performance. This includes the ability to monitor employees' activities and progress throughout their assigned tasks. These tracking data enable managers to better understand individual performances, identify areas for improvement, and acknowledge successes.
Workstation
Within a manufacturing ERP system, a workstation represents the location where production operations are carried out by employees. ERP software provides functionalities to manage and organize these workstations effectively. This includes task assignment to employees, scheduling work shifts, monitoring individual and collective performances, as well as managing the resources required for each workstation. Additionally, ERP systems can also integrate time management features, allowing employees to clock their work hours and enabling managers to track and manage worked hours.
Traceability and Inventory Management
Product Traceability
Products can be easily traced back to their original material through product traceability. This is a highly important feature, especially when there is an issue with a finished product. Parts can be traced with a lot number, and all products with that specific component can be marked or recalled. They can be tracked by batch or serial number. A product's serial number is a unique quantity of a product, whereas a lot number is how we reference multiples of the same product.
Quality Controls and Alerts
ERP software enables you to manage alerts and quality controls. By managing quality controls, problem areas can be quickly identified, resolved, and prevented from recurring.
Per Product
Subproducts are the result of remaining materials left by a particular component. ERP software facilitates subproduct management by allowing your bill of materials to include multiple products.
Integration of IoT (Internet of Things)
The IoT, or Internet of Things, refers to a network of physical devices equipped with sensors, software, and other technologies connected to the Internet. These devices can exchange data with each other and with computer systems such as ERPs.
Real-Time Monitoring and Maintenance
Integrating IoT into the ERP system enables continuous monitoring of production equipment through smart sensors. These devices collect real-time data on the condition of machines, detecting anomalies before they cause interruptions. This allows for proactive maintenance and reduces downtime.
Streamlining Production Flows
By connecting machines and sensors to the ERP system, companies can monitor every stage of the manufacturing process in real time. IoT data provides increased visibility into equipment performance, task progress, and the quality of products in production. This transparency enables managers to make informed decisions and implement immediate adjustments.
Integration with Other ERP Applications
Close coordination between manufacturing and sales is crucial for effectively meeting market demand and ensuring optimal inventory management. ERP systems facilitate this collaboration by providing integrated functionalities that enable smooth communication between manufacturing and sales teams.
Manufacturing and Sales Relationship
Manufacturing and sales are closely tied to replenishment rules. In Odoo, Reordering Rule refers to a rule that triggers the purchase of a product when the stock reaches its minimum level. These automated orders in an ERP system result in the creation of multiple units instead of just one.
This occurs in situations where creating a single product on order is inefficient, and a certain threshold of products needs to be maintained at all times. Once the inventory reaches a certain number, let's say 5, the replenishment rule will be triggered to manufacture more products to replenish the inventory.
Utilization of Sales, Inventory, and Participant Applications
Sales, inventory, and manufacturing applications are key components of a comprehensive ERP system. They play an essential role in managing the day-to-day operations of the business, particularly in the manufacturing domain.
- Sales Applications: These applications enable businesses to efficiently manage the sales process, from generating quotes to invoicing. By integrating sales data with the manufacturing module, companies can plan their production based on customer orders, ensuring just-in-time production and increased customer satisfaction.
- Inventory Applications: Inventory management is a critical aspect of manufacturing. Inventory applications allow businesses to proactively track and control stock levels. By integrating inventory data with manufacturing processes, companies can optimize their production based on current stock levels, thereby avoiding surpluses or shortages.
- Participant Applications: Human resource management is a vital element of any business. Participant applications enable businesses to effectively manage employee data, including work schedules, timesheets, and individual performance. By integrating this data with manufacturing processes, companies can optimize the allocation of human resources based on production needs, ensuring efficient utilization of available labor.
The main modules of an ERP for the manufacturing industry
Billing and Payment Management
Create invoices, track payments, and optimize payment deadlines to maintain a healthy cash flow. Benefit from an automated solution that streamlines your billing and payment processes in the Manufacturing ERP software.
Business Intelligence and Reporting
Analyze trends, evaluate performance, and draw valuable insights from your ERP software to guide your company's growth. Make better decisions through in-depth data analysis and customized reports for the manufacturing sector.
Customer Relationship Management (CRM) and Sales Management
Cultivate strong relationships with your customers and increase sales with a comprehensive and efficient management solution. Track leads, automate sales processes, and personalize your communication to boost your company's revenue in ERP solutions for manufacturing.
Expense Report Management
Enhance expense report management for the manufacturing industry through the use of an ERP. Track expenses, automate reimbursements, and ensure employee satisfaction.
Financial and Accounting Management
Keep a close eye on your finances in manufacturing industry ERP sector with an ERP software ensuring your financial and accounting management. Manage cash flows, budgets, and financial reports for effective financial management of your business.
Inventory Management
Optimize inventory management and be prepared to meet all demands. Track stock levels, manage supplies, and minimize stockouts to ensure customer satisfaction.
Leave and Absence Planning
Ensure effective workforce planning by simplifying leave and absence management. Track leave requests, establish flexible policies, and minimize schedule conflicts to maintain high productivity in the manufacturing ERP software.
Manufacturing Planning and Tracking
Plan and track your production in your ERP to optimize supply chain efficiency and ensure product quality. Manage work orders, track production times, and ensure timely delivery to meet the requirements of customers in manufacturing industry ERP.
Personnel Administration
Enhance employee performance and satisfaction with simplified HR management. Manage their data, automate administrative processes, and ensure regulatory compliance to establish transparent and efficient personnel management in the manufacturing sector.
Purchasing Management
Simplify the procurement process to reduce costs and optimize operations in the ERP for the manufacturing sector. Automate workflows, manage suppliers, and optimize purchase contracts to ensure the quality of products and services.
Quality Management
Ensure compliance with the highest quality standards in manufacturing industry ERP. Identify and correct non-conformities, track performance, and guarantee customer satisfaction by delivering superior quality products and services.
Choose the right ERP for your business !
Odoo ERP
Odoo stands out as an adaptable ERP solution, offering a comprehensive suite of modules for production management, resource planning, inventory management, and procurement. Its flexibility allows for customized configuration, thus meeting the specific needs of manufacturers across various industries.
Odoo GOLD PARTNER
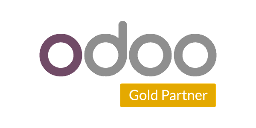
- Worldwide ERP solution
- Based Cloud ERP Solution or On Premise ERP Solution
- Prices per users
- Adapted for small businesses and mid-market businesses
- +40 000 apps availables on Odoo Marketplace
Cegid XRP Flex
Cegid XRP Flex stands out for its ability to integrate third-party solutions and adapt to regional and international requirements, making it an ideal choice for manufacturers operating in a globalized environment. With its advanced features for operations management, production planning, and performance tracking, it provides manufacturers with the tools necessary to enhance their efficiency.
Cegid Partner
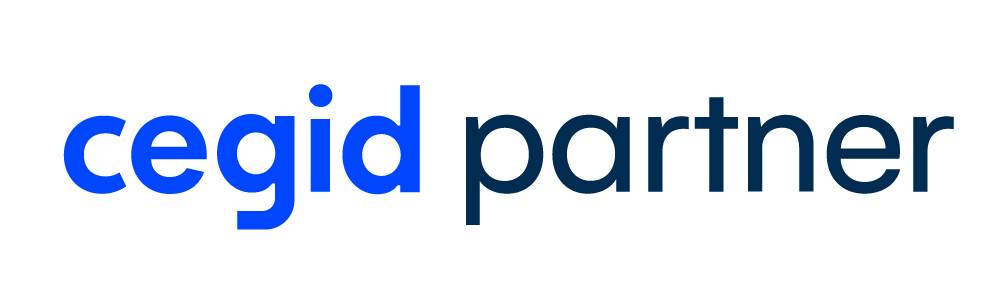
- European ERP solution
- Based Cloud ERP Solution
- Prices per ressources
- Adapted for Mid-Market Businesses
- +30 apps availables on Cegid Marketplace
The activities of companies in the manufacturing sector
Here is a list of manufacturing sectors:
Automobile
Companies manufacturing cars, automotive parts, tires, etc.
Aerospace and Defense
Production of aircraft, defense systems, spacecraft components, etc.
Electronics
Manufacturing of electronic components, consumer electronic devices, telecommunication equipment, etc.
Food and Beverages
Businesses producing processed foods, beverages, dairy products, confectionery, etc.
Chemical and Pharmaceutical
Manufacturing of industrial chemicals, medicines, healthcare products, etc.
Textile and Apparel
Production of clothing, textiles, fabrics, leather goods, etc.
Construction and Building Materials
Companies producing construction materials such as cement, bricks, tiles, insulation materials, etc.
Energy and Environment
Production of energy equipment, renewable energy production systems, components for waste management, etc.
Captivea, Your ERP Integrator to Guide You
Launch your project with us now !
As a leading Odoo integration specialist, Captivea has a deep understanding of this versatile ERP platform, enabling it to offer tailored solutions to meet the specific needs of each business.
Our team emphasizes close collaboration with clients, understanding their business objectives, and working in partnership to implement ERP solutions that perfectly meet their needs. With a qualified team, we are committed to supporting businesses in their long-term success.
Faq For ERP manufacturing industry
ERP for manufacturing sector integrates various business processes into a unified system, enhancing efficiency and productivity across all levels of production.
ERP systems streamline manufacturing operations, improve inventory management, and optimize supply chain management.
ERP software solutions offer comprehensive tools for managing manufacturing processes and enhancing business intelligence.
Manufacturing ERP systems include modules for inventory control, warehouse management, and production scheduling.
ERP systems optimize manufacturing operations by providing real-time data insights and facilitating supply chain optimization.
ERP systems are beneficial for various industries, including automotive, aerospace, electronics, and more.
Cloud ERP solutions offer flexibility and scalability, ideal for small manufacturing companies seeking affordable ERP solutions.
ERP systems play a crucial role in supply chain management by optimizing inventory levels and ensuring timely production.
ERP enhances business intelligence by providing analytical tools to evaluate performance and make informed decisions.
Integrating ERP with CRM improves customer management and enhances customer relationships.
ERP for project management streamlines processes, allocates resources effectively, and ensures project success.
ERP systems support business processes by automating workflows and enhancing operational efficiency.
ERP systems are essential for modern manufacturing to maintain competitiveness and drive growth.
Cloud-based ERP systems offer real-time data access, cost savings, and scalability for manufacturing industries.
ERP aids in inventory management by automating stock tracking and optimizing inventory levels.